Working Model 2D
2D Dynamic Motion Simulation
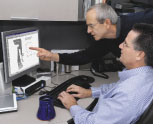
Working Model Helps Advanced Structures Technology, Inc. Analyze and Model Life-Saving Device
Traditional helicopter restraint harnesses, designed to maximize a helicopter pilot or crew members safety in the cockpit, are often restrictive. As a result, pilots and crew members frequently loosen the restraint systems to gain comfort and mobility. In the event of a crash, a loosened restraint system compromises occupant safety.
To address this problem, the U.S. Department of Defense awarded Advanced Structures Technology, Inc. (AST) a Small Business Innovative Research Program contract to design a helicopter crew member pretensioning device (PTD). The PTD enables pilots and crew members to wear restraint systems comfortably until a crash onset, when it automatically tightens around the occupant to reduce injury or improve the chance of surviving a crash.
Based in Phoenix, Arizona, AST began in 1986 as an engineering services organization and has maintained an average annual revenue growth of 30 percent. AST has expanded its service to include design and manufacture of custom compressors, manufacturing machinery, thermocouples, and pressure probes. The companys clients include TRW Safety Systems, Intel, AlliedSignal Aerospace, Hewlett-Packard, as well as many small and mid-size companies.
Understanding a Body in Motion
According to AST, two-thirds of helicopter crash-related injuries and deaths are due to upper torso flailing, leading to striking or being struck by objects or structures in the cockpit.
Before AST could design a pretensioning device, the companys engineers needed to understand how a body moves through space during a crash. AST engineers used Working Model® dynamic analysis software from Design Simulation Technologies to define the occupant "flail envelope" the body displacement envelope likely to be traversed by a helicopter crew members body during a crash.
"We tried a couple of other simulation computer programs, but didnt have much luck with them," says James McLellan, AST lead engineer. "We paid one consultant $5,000 for training on one product and spent almost a month trying to use it, without success."
Dynamic Analysis of the Flail Envelope
"When we discovered Working Model, one of our engineers went through the tutorial manual and was up-and-running in one or two days," McLellan continues. Whats more, Working Model paid for itself on the first use."
To define the flail envelope, McLellan and his colleagues used Working Model to analyze the main components: the human, the seat and floor structure, and the restraint harness.
AST calculated flail envelopes for three different harness conditions, all with the occupant in the same initial position. The first condition had the harness snug on the occupant to simulate a properly tightened harness or a pretensioned loose harness. The second condition applied a 200 lb. preload to the shoulder harness to simulate a pretensioning event on a snug harness. The third condition AST analyzed had four inches of slack in the harness. In all cases, the flail envelopes of the occupants head, hands, and feet were tracked so that comparisons could be made.
Some of the Working Model features that came into play for the PTD project included modeling of pin and slide joints, linear and rotational springs, ropes, irregular shaped masses with user defined mass and inertia, and input of force, displacement, velocity, or acceleration boundary conditions. With Working Model, engineers were also able to define which masses collide and which can pass through each other in a 2D view.
"Mathematically, without Working Model it would have been a nightmare to create the clear picture we needed to develop the PTD," McLellan continues. "Working Model uses a numerical methods approach to solve the equations of motion."
Occupant Model
To create the flail envelope with Working Model, AST engineers conducted dynamic simulations using a 50 percentile male patterned after the GM Hybrid III crash test dummy, a 5-foot, 8-inch tall, 163-pound person. For the human model, AST added a five-pound helmet to represent a military flight crew personnel.
AST obtained the seat geometry by measuring a crashworthy armored Navy helicopter seat. Next, AST modeled the floor structure as a horizontal projection of the floor under the seat with no changes to represent an angled floor, forward bulkhead, or control pedals. This approach gave AST the largest foot flail envelope. To obtain the largest head and hand flail envelope, AST did not model the panel, windshield, or ceiling. McLellan and his colleagues modeled the seat and floor structure as a single unit and gave them slide constraints to enforce motion only in the crash direction.
The model uses a five-point restraint harness consisting of shoulder harnesses, seat belts, and a crotch strap. The harness uses a webbing that has a 7.5 percent elongation at 3,000 lbs. load, and these values were used to get a linear spring rate for the harnesses in the model. AST used spring elements to model the crotch strap and seat belts. McLellan modeled the shoulder harness as a rope with a spring attaching it to the seat back. The rope has a collection of balls on it to model the harness-to-body contact, since the rope elements would otherwise pull through the body parts.
The short spring connecting the rope to the seat back has the spring rate adjusted to represent the total spring rate of the shoulder harnesses. The spring was run with no initial deflection when determining the flail envelope with snug harnesses.
To define the flail envelope with a 200 pound preload on the shoulder harness, the shoulder harness spring was given an initial deflection. For defining the flail envelope with a four inch loose shoulder harness, one of the rope sections had four inches added to its rest length.
Designing a PTD
After in-depth analysis and simulation with Working Model, AST engineers had a clear understanding of how an occupant moves through space in the cockpit during a crash. Armed with this knowledge, AST engineers designed a PTD that retracts four inches of shoulder harness slack in less than 35 milliseconds after crash onset, and then locks the strap, significantly reducing the occupants flail envelope.
AST is optimistic about the devices potential. The PTD is designed to be unobtrusive to crew members during normal flight operations, improving the pilots ability to operate the aircraft during maneuvers, strong turbulence, or gun recoil. The PTD also offers a unique recycle feature, which permits pretensioning multiple times during a flight. This way, pretensioning occurs in severe turbulence or during impacts that would not be classified as crashes.
The device may become an enhancement in future aircraft or a retrofit for existing helicopters, according to McLellan. AST also developed an electronic crash sensor to activate the PTD. The U.S. Navy may be interested in the PTD and crash sensor to improve helicopter safety.
"Its been an exciting project," McLellan concludes. "Were pleased that the PTD offers a solution for reducing crash-related deaths and disabling injuries."