Dynamic Designer Motion
CAD Embedded Motion Simulation
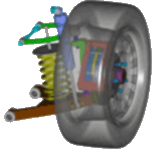
Simulation of Cam-Driven Machines Reduces Hardware Testing
Machine Design Services relies on Dynamic Designer to design and test very complex cam-driven machines.
|
||
"We use Dynamic Designer to simulate every mechanism that we design," explains Glenn Jordan, president of Machine Design Services (M.D.S.) in Boxborough, MA. Functional virtual prototyping is a critical part of their0 design process, and they enjoy the benefits they get from Dynamic Designer. M.D.S. designs and builds automated assembly machinery. With a broad background in machine design, they work in virtually all industries. They are experts in synchronous machinery design and often work on machines that process more than 100 parts per minute. Complex, high-speed, multiple cam-driven mechanisms are at the core of most M.D.S. machines. The complexity of the designs makes physical testing difficult and cost-prohibitive, so they had to integrate virtual prototyping into their process. Today all M.D.S. machines are developed in a paperless office using 3D CAD and Dynamic Designer. Mid-Range CAD is fundamental in the design and development of accurate 3D solid models. Dynamic Designer seamlessly extends CAD systems to test the characteristics and functionality of the design before the machine is built. The benefits of using virtual prototyping throughout the design process at M.D.S. are reduced physical testing costs, reduced development time, and the production of more reliable machines. As Jordan explains, "Dynamic designer has reduced the time and money we spend in the proof-of-principles portion of our projects." |
||
Step by Step Functional Virtual PrototypingA typical M.D.S. mechanism involves three to six cams resulting in complex high-speed motion. These mechanisms are assembled into complex machinery. M.D.S does not cut any metal, mold any parts, or construct a prototype for a machine until it has been simulated with Dynamic Designer. STEP 1. The process begins by modeling the kinematics of a design concept. Dynamic Designer animations and plots are used to make sure the model matches the timing specified in timing diagrams. Tracing the output of cam-driven levers verifies stroke or displacement characteristics.
STEP 2. Dynamic studies are utilized to understand accelerations at important locations. Acceleration information helps specify the range of component masses required to keep the forces in check. STEP 3. Next M.D.S. uses CAD to create a complete 3D model. The accurate mass properties in the 3D model are critical to the virtual prototyping process for the calculation of force quantities. STEP 4. When the 3D model is complete, they utilize Dynamic Designer to calculate forces on bearing levers and other locations. STEP 5. In high speed machinery design, it is important to minimize stroke, which often causes clearance problems. Typically, design motions are not rectilinear and there may be three or four cams contributing motions to the mechanism. It is very labor-intensive to check the position of these mechanisms throughout each 360-degree position of the machine timing. Viewing the Dynamic Designer animation in 3D is often the only way to check for clearances around nests, especially when the parts being picked and placed are oddly shaped. Realizing the BenefitsBy using Dynamic Designer M.D.S. is saving time, money and developing better product. M.D.S. uses animations to effectively communicates design concepts and proposals to customers. "We often share animations with our customers so that they can see the mechanism move and better and understand what is happening," explains Jordan. In fact, M.D.S. is now offering machine animation creation as a service to customers. The animations can contain plots to show engineering information or can be accompanied by an exported Microsoft Excel file containing the plots.
Virtual prototypes can only replace physical tests if the results are accurate. "We have checked the data we extracted from our Dynamic Designer model against the actual machine and feel very comfortable with the results," states Jordan. Jordan in turn can create accurate proposals and make important design decisions without building and testing a physical prototype. "I am finding that as my confidence has grown using Dynamic Designer, I have been able to do some projects lately that I may have walked away from before because of the unknown cost of development," explains Jordan. "I do virtual prototyping to get myself comfortable with an idea for a mechanism, before I invest the time in pursuing a more detailed study of the design details." M.D.S. has embraced the power of virtual prototyping. In their continual quest for the paperless office, they plan on integrating more and more Dynamic Designer-type technologies into their processes. |