Working Model 2D
2D Dynamic Motion Simulation
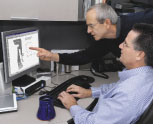
Engineering Consultant uses Workign Model 2D to prepare for Deep Sea Exploration
Deep sea explorations are awesome events often involving the wildest of Mother Nature’s children: gale-force winds, pounding waves and powerful currents and temperature extremes. While these elements cannot be tamed, dynamic analysis software can show their effects on ships and ocean engineering equipment. Ed May, an engineering consultant, uses Working Model® 2D dynamic analysis software from Design SImulation Technologies, Inc., to prepare for the worst case scenarios in his ocean engineering work. As a result, May is reducing time spent on generating complex equations, tightening design cycles and producing safer apparatus.
May, with nearly 20 years of working experience in military and marine engineering, provides design, engineering and consulting services for complex marine engineering projects. Currently, his primary client is Oceaneering International, a company that provides engineering services and hardware to customers operating in marine, space and other harsh environments. May has previously worked for companies that include the Tennessee Valley Authority, Lockheed Martin and NASA's Goddard Space Flight Center. He provides engineering consulting services from his office in Columbia, Maryland.
Working Model Software’s Versatility and Flexibility Realized
"Working Model has significantly reduced the time I spend on cumbersome and tedious tasks," says May. He considers Working Model’s ability to automatically generate equations as its key feature. Today, he can complete a final motion simulation in two to three weeks compared to well over a year with manual calculations.
In the past, May wrote equations manually. "It was a pain," he remarks, "and I was never able to show my work graphically." He says that Working Model is extremely helpful in communicating effectively with his customers who want to see May’s work rather than look at calculations.
"Working Model does everything I need to do for my work. Its flexibility is incredible. The fact that it is integrated with AutoCAD® from Autodesk, Inc. is a plus for me. Also, Working Model’s dynamic link to Excel® software from Microsoft Corp. enables me to write my own PID (proportional integral derivative) controller equations for control theory."
Perils of Deep Sea Exploration
May recently used Working Model for dynamic simulation of an off-loading crane that is used for lowering a 30,000-pound manned submersible for deep sea research from a 200-foot ship. May had to keep track of many factors, including heights of waves, motions of the ship, loads occurring in the lifting device caused by the waves and the ship’s motion, and the crane’s cable tension. He also needed to determine specifications for motors, winches and other components essential to the design of the crane.
Dynamic Analysis
May required dynamic analysis software tools to find out how those forces affect each other over time. For this off-loading crane design, May needed to include equations to determine drag forces; forces caused by motion from the moving ship; entrained water forces (which increase the inertia of the vehicle); effects of the submersible at the water surface; and buoyancy force. Ultimately, he wanted to model the relative motions between the vehicle and the ship at the area where the air and sea meet.
To begin this complex motion simulation assignment, May first sketched out sizes and shapes of entities that he wanted to model in Working Model 2D. Next, he used AutoCAD® to create detailed drawings of the parts, which he later imported into Working Model. While in Working Model, he applied dimensions of size and mass of the submersible, and then used Working Model to calculate inertia of the submersible and vehicle. He used AutoCAD to design hardware, such as motors and winches.
Once May generated equations and entered them into Working Model, he also put in types of motions for the ship and ran the simulation. He modeled exactly what happens to the submersible when it is lowered into the water. Working Model then calculated the amount of drag caused by the submersible entering the water while the ship moves, and the tension of the cable in the choppy ocean waves.
The graphical output provided by Working model allows May and his clients to visualize the motions of the vehicle during launch and recovery. For example, he looked at the effects of changing the tension in the cable which lifts the heavy submersible out of the water as the ship pitches in the waves. Using this method, he can design the crane, cables and vehicle for the worst case scenarios. Looking at these forces, he modeled the potential effects of various ship motions caused by different wave heights and then designed the necessary boom, cable and other components for the safest off-loading system.
May further experimented with different scenarios by graphing the various forces in Working Model and then inputting specific data from the client. If design parameters change, May easily inserts new data such as sizes, mass and weight to rerun another simulation.
Greater Engineering Assurance
"Without dynamic analysis simulation software, engineers are left to guess at safety factors and ultimately they are never sure of their designs until building prototypes," comments May.
"With Working Model, companies can do a lot more analysis than ever possible. In addition, I use Working Model as a key software tool in presentations to prospective clients. I can show them a motion simulation within a few days of our first meeting, and most are amazed at what the software can do," he adds.
"Engineers like myself can achieve accurate and realistic analysis of forces, weights and strengths before anything is built," he notes. "We can escape the rut of building and breaking prototypes to make designs work. With Working Model, simulations and experiments are easily accomplished on a computer screen. As a result, shorter design cycles deliver better and safer products to market faster."